Introduction
In oral solid dosage (OSD) manufacturing, powder blending is a key requirement for achieving a uniform composition and ensuring that the correct amount of Active Pharmaceutical Ingredient (API) is dosed in the final drug product. Powder blending involves three primary mechanisms including convection, dispersion, and shear mixing. Macromixing (or convective mixing) refers to the bulk movement of powder components within a blender. While it contributes significantly to the overall blend uniformity, it rarely results in a homogeneous mixture on its own. Micromixing (or dispersive mixing) occurs simultaneously in most blenders. This mechanism breaks down smaller API agglomerates and distributes them evenly throughout the blend. Dispersive mixing typically takes longer to complete than convective mixing.
Once both convective and dispersive mixing are achieved, the powder blend can be considered homogeneous.
As an integral part of the Quality by Design (QbD) approach, comprehensive process understanding plays a crucial role in continuous manufacturing to ensure the quality of intermediate or final products. By enhancing product knowledge and process control, a drug product shall be consistently released with the intended quality. In this regard, Process Analytical Technology (PAT) tools, such as Near-Infrared (NIR), offer non-destructive and non-invasive approaches as both quantitative and qualitative analysis tools.
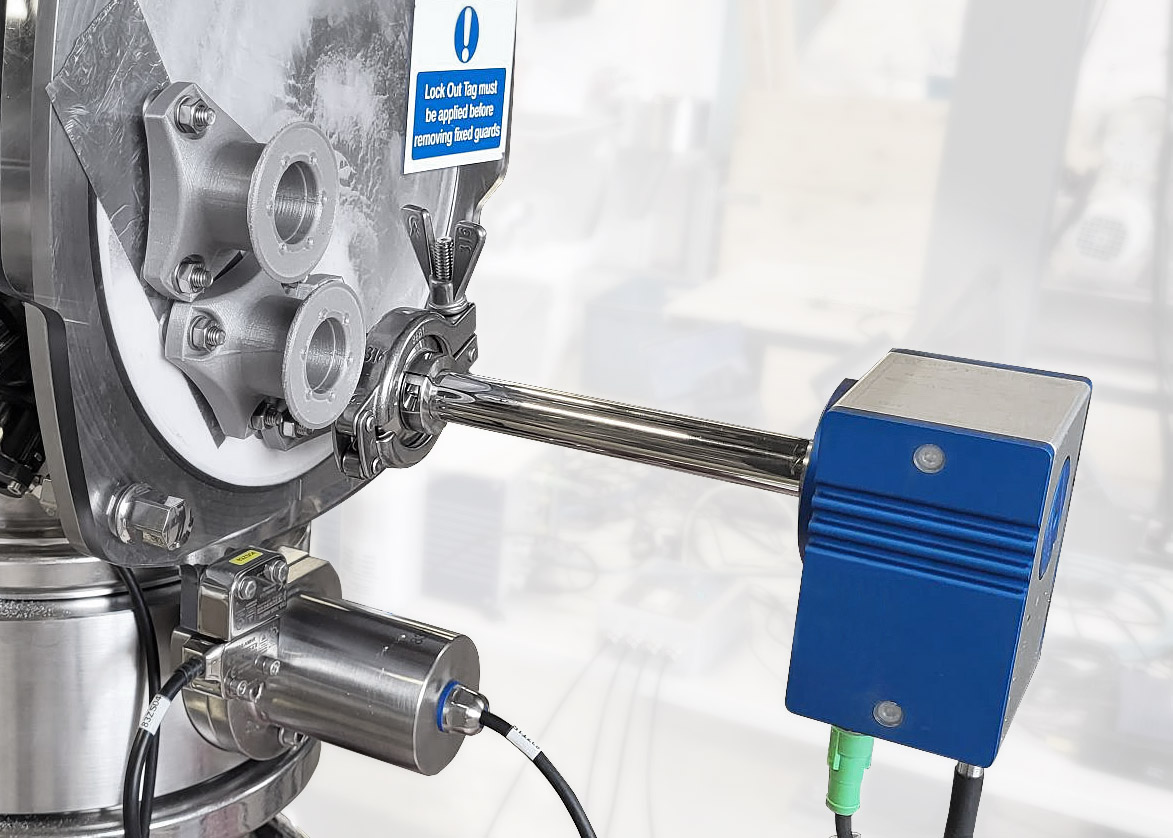
This study investigated the integration of in-line NIR spectroscopy into a semi-continuous blending process to monitor blend uniformity under varying process conditions. The system used for this study was a SentroPAT FO NIR covering the wavelength range 1100-2100nm and a SentroProbe DRLS which was installed in a Gericke Mini Batch Blender. A low-dose binary formulation containing 2% w/w caffeine as API was used.
Two analyzing methods were applied and compared for endpoint detection:
Partial Least Squares (PLS) regression
Moving Block Standard Deviation (MBSD)
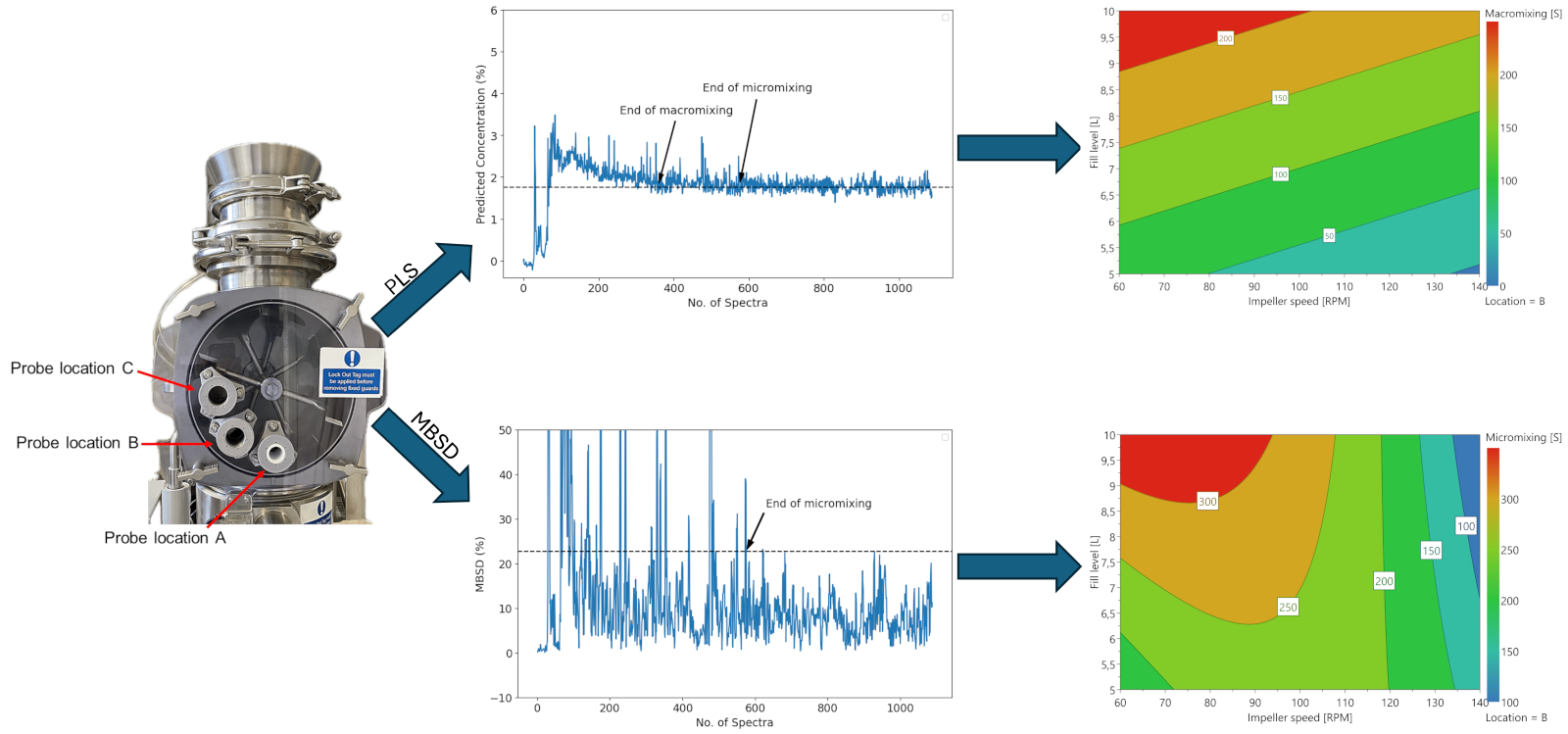
Key findings
While PLS modeling enabled real-time prediction of blend potency levels, indicating an endpoint of macro-and micromixing, it was sensitive to variations in powder behavior under different process conditions. In contrast, the MBSD method exhibited more robustness against such variations during semi-continuous blending but could only provide the endpoint of micromixing.
By evaluating the detected endpoints across different blender conditions, an increasing impeller speed significantly shortened convective mixing times, while larger powder volumes led to longer mixing times. For dispersive mixing endpoint, higher fill levels only extended blending time at lower impeller speeds.
In conclusion, the study showed that qualitative NIR spectra could be measured and demonstrated that in-line NIR monitoring can significantly improve process understanding of a semi-continuous blending process.
Feel free to contact the author or explore additional information in the slides presented at international conferences.